Racing is Expensive
I read Jalopnik regularly, so I became aware this morning of the link they posted to Speed:Sport:Life about the expense of racing. I’m still not totally sure what the purpose of the article is, I guess it’s just to educate people who weren’t aware- and I guess that’s reasonable enough. I have always assumed that real racing is very expensive, but I appreciate the concrete compilation of forms of amateur racing, and their approximate costs.
The author’s brief discussion of LeMons was most interesting for me, having participated in the entire process of preparing and racing a car. My team was really cheap. We didn’t have very much money to spend, and cut just about every corner we could. I would estimate that we invested less than $1500 on the car, all inclusive. We used the original seat, junkyard rims, really cheap tires, and built the roll cage ourselves. We borrowed a trailer, towed with one of our own vehicles. We splurged and rented an RV, but including absolutely everything, I think each of the five of us spent less than $1500, and that’s starting from scratch, owning nothing relevant to the endeavor except mechanics tools and our personal cars. And now we own a (still functioning) car with a cage, as well as all the personal safety equipment to do it again. If When we do it again, I think we should be able to spend less than $500 each.
Like I was wondering about the S:S:L article, you may be wondering what my point is here- I guess I don’t have a point anyways. I think the author was a little harsh on the value of a LeMons event, and I would disagree that “buying a seat” on a LeMons team is the way to go- besides simply “seat time” I think the LeMons preparation and event experience was a big challenge to learn how to better work with my team (my friends), and as really my introduction to anything having to do with car racing, gave me a lot of information, fast, about how it works- all in an setting where people are (generally) tolerant of your inexperience. So, $1500 for 1.5 hrs of “seat time” isn’t that great by the S:S:L author’s benchmarks- but there was a lot more value than just “seat time” in lemons, for me.
Yesterday I went and checked out the San Fransisco Region SCCA autocross event at the coliseum in Oakland. I was pretty impressed by the scene, there was a good mix of totally stock cars and totally race cars, with a wide spectirum of driving skills not necesesarily paired with the raciness of the cars- in other words there were some great drivers driving mostly stock cars and some crappy drivers driving nicely speced out cars- and a broad range of other car/driver pairings. People were generally friendly once I got the courage to actually introduce myself and engage them, it was generally a nicely spirited, noncompetitive, friendly, well organized event. I’m sure if the S:S:L author had included it on his list it would be described as “not real racing” as LeMons was, but it is reasonably cheap and is a good time- and a reasonable way to get into performance driving. Just because it’s not on a track and not for long distances or durations doesn’t mean it’s not worthwile for beginners, and it’s pretty clear many people have made a serious, long-term commitment to particularly this form of racing. It’s not a “seat time” bargain either- $35 plus dues for 10 min max?
I got rides around the course with a guy and his ’99 M3 and a different guy (Jason) and his ’93 white track Miata (suspension, exhaust work, wheels and tires). The M3 guy was pretty conservative- I think it was his daily driver, and it was his first time autocrossing. Despite that, it’s a quick car, not the slowest one out there. Jason is something of a regular, as far as I could tell- he’s not the fastest or most skilled driver, but he has the ability to drive the car hard without worrying that it won’t be able to get him to work the next morning and is working aggressively to improve his skills- that is to say, his driving was much more spirited than the M3’s drivers was… The Miata really is an excellent car- it was really fun to be in the passenger seat while Jason pushed the boundries of the traction around tight corners. It’s a fraction as powerful as the M3, but barreling through a slalom wide open you’re likely to forget that. He also spun it once- bringing back pleasant memories of LeMons.
So I’m looking forward to taking a car to the autocross to drive- soon- and there are at least five over the summer that are located at the Golden Gate Fields lot, 1 1/4 mile away from my house. I think the EV Miata should be an interesting AutoX contender once I get it put together… I’m not dissapointed by the S:S:L article’s harsh reality check- there are plenty of cheap racing options for me now. Someday when I’m more loaded (haha) I can consider the “real” ameteur racing options described.
In: LeMons, Life and Times, Racing
Impression: 2009 Mercury Grand Marquis
In Colorado over the weekend my Dad and I rented a car- since the rental car lot was out of subcompacts, they gave us an automatic “upgrade” to a “premium” level vehicle- a nearly brand new Grand Marquis. While providing useful transportation all weekend, the Marquis (pronunciation informally decided to be “mar-kees”) was also much more interesting than a subcompact could have been. Heck- the Crown Vic is practically american car legend! The car has a significant cachet. It’s a classic, iconic car.
That all said, it’s also a piece of trash. I will procede to numerically compare it to my benchmark of internal combustion automotive perfection- the 1994 Toyota Camry Station Wagon LE V6 (AKA Pimp Wagon)
Area of interest | Camry | Marquis | Marquis W.R.T.* Camry |
---|---|---|---|
Cylinders | 6 | 8 | 33% More |
Displacement | 3.0L | 4.6L | 53% More |
Horsepower | 188 | 224 | 19% More |
Camshafts | 4 | 2 | 50% Fewer |
Curb Weight | 3263 lbs | 4117 lbs | 26% More |
EPA Mileage | 18 | 18 | Same |
KBB Value | $2,860 | $28,606 | 900% More |
Starting to get the picture? The Marquis sounds like a cop car and rides very comfortably on the road- but I was expecting a whole lot more grunt when you really mash the throttle and get the revs up. Even burying it deep in the carpet, the Camry is much more responsive and pulls harder. The ‘quees’s steering is very light and brakes are firm, suspension is akin to a chinese bean cake- squishy.
I was impressed by the Marquis’ lack of interior space, particularly legroom–
Area of interest | Camry | Marquis | Marquis W.R.T Camry |
---|---|---|---|
Front Legroom | 43.5 in | 41.6 in | 4.4% Less |
Rear Legroom | 34.7 in | 38 in | 9.4% More |
Exterior Width | 69.7 in | 84.5 in | 21% Greater |
Total interior and cargo space | 140.8 cu. ft. | 128.1 cu. ft | 9% Less |
So, the Marquis, despite being a much larger car has less front legroom and less usable space. It’s also insanely wide. As you can tell, I have a high opinion of the Camry- but let’s see how the Marquis shines with the really important stuff-
Area of interest | Camry | Marquis | Marquis W.R.T. Camry |
---|---|---|---|
Cadavers Stashable | 1 small one | 5+ big ones | 400% More |
Number of rear wipers | 2 | 0 | ∞% Fewer |
Likelyhood of being
mistaken for cop |
Very unlikely | Quite likely | 5 Doughnuts More |
Stereo | Bangin’ | Lacking | Are you kidding? |
Likelyhood of being ignored | Very high | Less | Depends |
Americanness | Somewhat | Absolute | Pure Red White and Blue |
So, the Grand Marquis is a car to respect and enjoy- in its own way it’s really wonderful. It is a classic, iconic, instantly recognizable vehicle backed with decades of American bench-seat cruiser history. It’s also a design that seems absolutely stuck in the ’90s. The dashboard is huge and impedes footroom enormously. The front middle seat is cramped and the cupholders and lighter are effectively inaccessible when it is occupied. The built in trip computer falls short of expectations, doesn’t realize it’s potential. There are many more modern cars that are much more functional and innovative than the Vic/Marquis available at the price point. Not to mention that you could have a whole fleet of Camry Wagons.
Regardless, no cars have the cachet and iconic status of the big Ford. I respect the car, but I would not want to own one. I am grateful that I got the unexpected chance to get to know the Marquis over the weekend, the experience wouldn’t have been the same with a Focus or dinky Kia, one of the bland throwaway subcompacts so popular with rentals. The Mercury may be technologically behind, but it’s not a throwaway piece of crap- I feel grateful to have participated in the American legend that is the Crown Vic.
*(W.R.T. = With Respect To – have you ever been in a college math class??)
Circuit FAIL
First- the good news.
The circuit boards came in from Gold Phonenix, it really is very easy to order from them, and I am pretty happy with the quality. I first contacted them on March 13th (Friday), asking for quote confirmation for a 155 in^2 “Special Price” order, including the gerbers in a .zip file and my location (California). I was given a quote on the 15th (Sunday). I sent the money via PayPal, with my shipping address and the name of my .zip file. I was notified that the order was processed on the 16th (Monday). A shipping notice with tracking number was sent on the 23rd (the next Monday), and I recieved the boards this morning. That’s roughly 12 days.
The boards look quite good, all the traces and through plated holes stand up to visual inspection. The silkscreen is not very well alligned, and has minor smudging in a couple places.
I was quoted for 2 8″x8″ panels, with 4 boards each, and recieved 3, for a total of 12 boards, 168.75 in^2. This is in line with other reports I have read of GoldPhonenix delivering more than you might expect. Fine with me! These boards ended up costing about $10 each, $.71 per square inch. Really good deal.
My order of parts from Digi-Key arrived over the weekend. It has now taken the record of biggest Digi-Key box yet from the prototype parts shipment.
Better yet, I managed to order all the parts I need! Planning pays off.
So far so good, the power supply section of the board works just fine-
and the ICSP works just fine
The power transistor footprints look good, I picked up some 3/8″ long 4-40 machine screws and nuts- looks pro
So, where’s the dramatic tension? Why is this post named “FAIL”? Because I screwed up the circuit- take a good look at that first image, DUH, I swapped the connections to C and E. It’s so clear now. Oh well, I can live with a little re-work. Gives it character. Everything else seems to work well. I’ll fix that, and fix my minor screwup with the silkscreen labels of the faston terminals- CONN_1, CONN_1, CONN_1… is not very descriptive. I thought I had fixed that- KiCad un-fixed it when I reread the netlist. CONN_1 is the default value of that schematic element, and by default it is not printed in the schematic- so you have to double click on the schematic element, go to “Fields” then select “Value” to change it. You can change the text in pcbnew (be sure you change the value, not the reference), but it will revert to whatever Value is in the netlist if you read the netlist in.
I also replaced the current limit resistors on all the LEDs with 470ohm instead of 220ohm, except for the (blue) power LED.
I think we can make this work.
Battery Regulator- The Next Step
I finished the new board design a few days ago- I don’t think I’m an expert or anything, but definitely did a better job this time than I did on the prototype- Just to begin, I checked my schematics and footprints carefully. That in itself will make a big difference! I also got the overall size way down- from almost 24 in^2 to about 14 in^2. I spent some time refining and fixing up the silkscreen for usefulness and legibility, and ran DRC tests. I have at least 8 mil clearance throughout the board- It’d be nice to have more, but it is sufficient for the requirements of the board house. I ended up running a bunch of traces between pins of headers and DIP chips.
As with many projects, in order to move things along it’s now time to buy stuff.
- I contacted Gold Phoenix’s sales rep to arrange an order of the final circuit boards. I think I should be able to get 10 or 11 boards for $99- an excellent deal.
- I recompiled my BOM and made a digi-key order for all the parts necessary for populating another 5 boards- $68 dollars worth of wirewound resistors! Over $250 total.
- I purchased LEDs, fuses and heatshrink from MPJA, I still haven’t decided exactly what LEDs are going to be what colors, but I knew I needed a bunch of reds and greens.
- I bought a buch of 1/16 aluminum sheet on eBay, I can use a shear at school to cut it to make base plates for the regulators- I’m planning a setup kind of like this:
I also ordered four 80mm fans on eBay to mount over the resistors. I decided it was totally worth it to get the blue LED versions.
- And, I ordered a Fluke 377 current-clamp multimeter. Besides always wanting one, I will use it to monitor the charger when I figure out how to control it via the REGBUSS port. I considered cheaper clamp meters, but the conclusion I drew from reviews online was that the Fluke was really the way to go. Expensive, yes.
- Oh, also I ordered a new FTDI board from sparkfun that will go right on the header I have on the reg board, as well as some little board with a RJ12 pigtail- meant for use with the PIC ICSP system, I will use for the REGBUS. And a Salae Logic analyzer. I think it will be useful.
So, am I some kind of high roller here? Spending all this money? No, but I have to finish this project right, and I am very lucky that my parents are supportive of my ambitions.
I am looking forward to testing this regulator system on a real battery pack- I think that’ll be coming pretty soon.
More CNC Thoughts
I’ve been thinking more about how I would I’m going to build a CNC mill. My earlier ideas have changed a bit, some a lot.
I’m not going to try to use servos, it is worth more to me to get the machine usable quickly, and the HobbyCNC stepper boards are pretty nice. It would also be an easy upgrade to hook it up to the step/direction signals from the KCam MaxStepper or DeskCNC board. These seem all like nicely developed, reasonably priced and reasonably effective solutions. I plan to use a big Chinese switchmode powersupply to power the HobbyCNC driver board, rather than the transformer/bridge setup they describe in the kits. You can pick them up for dirt cheap, and they are very easy to use.
I would still like to use a “CNC on a Budget” Z axis, I’m going to inquire about getting one of those, hopefully soon so I can use its design as inspiration for the other axes. I am pretty sure I want a gantry Y axis setup, but further than that, I’m really not so sure. I suppose I should probably start I just spent some time looking around at other’s machines on Google and CNCZone- it looks like bunches of people do the gantry arrangement with dual leadscrews at either side of the X axis (that moves the gantry up and down the table) I suppose that wouldn’t be too bad, just have to get a hold of some timing belt and pulleys. Then you really do have to have good thrust support bearings on the leadscrews also, since there won’t be any other thrust support from a directly connected motor- though I would avoid relying on that anyhow. I guess then I should continue shopping the eBay- see if any good deals come up on rails and trucks or rods and bearings. I think either would work fine. I like the idea of not having any important parts under the cutting table- I think it could increase the versitility of the mill greatly in some situations to be able to set it up on any sort of table material.
I found this site today and read through a bunch of their (excellent) content. Makes me think that using a single speed Porter Cable router, a variac, and their fancy chucks would make a pretty good spindle. There’s also lots of great info on there about bits in general and how to best use them.
I should probably hop on Sketchup again… see if I like it any better than I did last time I tried it. Or maybe I’ll test out SolidWorks. I’m in a class about AutoCAD right now, but I rather detest it- maybe I’ll draw this up in one of the aformentioned programs and then draw it in AutoCAD for my class project.
Anything’s better than just napkin sketches.
Battery Regulator- part 4
I finished testing the battery regulator board over the last two days, as I planned I did a full-current “burn” test and tested the MCP2551 (CAN transciever) based communications circuit. Things went mostly according to plan.
I had planned to burn in the power circuit for ~2hrs, but I got all the information I needed in about 15 minutes- the transistor is fine, by my calculations it should be burning no more than 1w (less with higher hfe optocoupler) which the datasheet specifies is OK without a heatsink up to ambient temperatures of 40-60 C. So, I will make thermal pads and bolt the TO-220 pads to the board, I don’t think a heatsink is necesesary.
The power resistor on the other hand didn’t fare so well. Just because a power transistor is rated “50w” doesn’t mean it can take a power close to that limit for a sustained amount of time without any thermal considerations. That resistor got crazy hot. 33 watts is a lot of power when it’s all going to heat in such a small area. The anodizing changed colors, the plastic plugs at the ends of the resistor expanded outwards and the solder melted causing the wires to slide around.
I cut the power when I noticed this, once it cooled down again the plastic plugs retracted slightly, but you wouldn’t mistake it for new- and the anodized surface is still a little darker than new resistors. It still reads an acceptable resistance though, so I’m not going to toss it.
When revising the schematic earlier I decided to nix the “Fan” output transistor, which after seeing this I have decided to add back in. I think if I mount the resistors on some aluminum plate and use some forced air everything should be OK.
About the MCP2551 CAN transciever, which I added to the schematic as an easy robust way to implement an EVILbus style communication bus (BatBuss) is a complex little guy- read that datasheet closely. I assumed it wouldn’t care how slow the baud rate on the bus was, so I could use it for even DC signals- that’s not the case though.
1.5 TXD Permanent Dominant
Detection
If the MCP2551 detects an extended low state on the
TXD input, it will disable the CANH and CANL output
drivers in order to prevent the corruption of data on the
CAN bus. The drivers are disabled if TXD is low for
more than 1.25ms (minimum). This implies a
maximum bit time of 62.5μs (16kb/s bus rate),
allowing up to 20 consecutive transmitted dominant bits
during a multiple bit error and error frame scenario. The
drivers remain disabled as long as TXD remains low. A
rising edge on TXD will reset the timer logic and enable
the CANH and CANL output drivers.
When I used another MCP2551 to check the onboard one by making a little sketch to toggle the “TX” pin every couple of seconds I got no output on the second transciever. When I set the sketch to toggle with 2ms cycle delay (effectively probably 300-500 hz) my multimeter read ~2.5v on the output of the second chip. This would idicate a duty cycle of 1/2 and is enough to make me think the chip is working right. This means my bit-banged “BatBuss” must run at at least 16kb/s- more challenges. At least I can leave that until later.
And voilà – I think I have enough information to redesign the board. When I have finished, and verified correct operation in service I will post the schematic and software, or at least software specifications. I have considered making this a kit also, since I wasn’t able to find these regulators on sale when I was looking, someone else may be interested in skipping this arduous design process!
I have been meaning to publish some of my older projects, as well as to make an about page, put up some links, and change or customize the CSS- look for all that soon.
CNC Thoughts
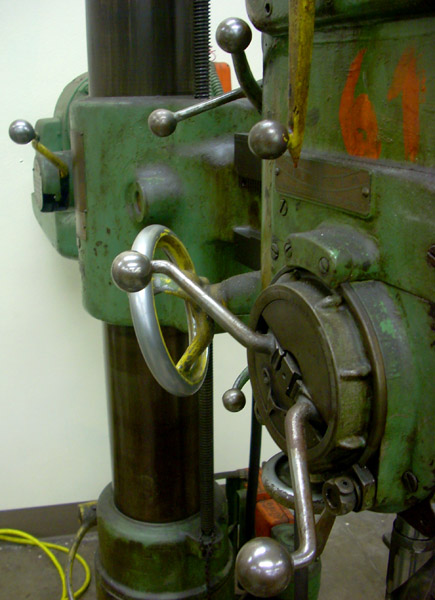
Drill Press, Laney College Machine Shop
Building a small CNC mill has been one of those projects I have thought about dozens of times over the years but have never initiated. It’s come up again now, and maybe this is the right time.
I would really like to be able to cut parts out of acrylic and aluminum sheet, as well as engrave text and mill out shapes. I can imagine many applications for milled acrylic as an enclosure for PCB based projects- potentially an asthetically pleasing, compact, cheap way of packaging a device.
So I’ve started shopping the eBay for linear motion parts, I would like to build the machine out of aluminum and use recirculating ball linear bearings and hardened rods, with Acme leadscrews. Great deals on new old stock parts can be found on eBay, but NOS bearings and rods are still pretty expensive, and are generally kind of a compromise between what you were actually looking for and what happens to be for sale. There are some parts on eBay now that I think would make a very nice set of axes, I have to decide whether they’re worth the (bit more than I’d like) price.
I am envisioning a gantry-type mill, using 24″ long rods, for a travel length of about 18″. An “Instant Z Axis” from CNC on a Budget is pretty tempting, as is their 3 speed spindle. I think his prices are very fair for the amount of material and work that goes into his products. So, a couple hundred dollars here, a couple hundred dollars on aluminum plate and linear bearings and you still haven’t got a CNC machine!
The most practical solution to simply getting a machine up and running would be to purchase a proven stepper motor based motion kit, like those from Hobby CNC. I would really like to go a different route though, I think stepper motors are a bit less than optimal- slow, noisy, generally not that elegant. Optimally, I would use any old brushed PMDC motors to drive the leadscrews, then attach a linear scale to each axis and run it closed loop servo-style. Capacative linear encoders are cheap and plentiful on eBay- search for “digital quill”. The data output on these is pretty well documented here and here, that’s not to say it wouldn’t be challenging to implement a system to read them and use them in a closed loop system with the motors. I bet it would work, though, possibly work well. I think it would be fun to build a custom control board with motor drivers, inputs for those scales and an onboard G-Code interpreter, then make a complementary app for the host computer that would work as a DRO and to feed the controller lines of G-Code.
Ok, not a small project. I should wait until I have a bit more machine shop experience then concentrate on building the machine and then pick up some steppers to get it running- the custom servo setup would be fun, though.
And, of course, I’ve got to finish the battery regulator system and the electric car first. But I’ve got a little cash burning a hole in my PayPal account, maybe it’s time to pick up some linear motion parts. Or maybe, as with so many ideas, it would be wiser to resist the impulse purchase and not regret it later- just like there are deals on eBay now, there will be deals later. Not an unusual quandary for me.
Battery Regulator- part 3
I have confirmed that the board programs and communicates correctly via serial with the Arduino environment. Almost everything is working as planned.
The timer that drives the PWM on pins 11 and 12 (ATMega168) or 5, 6 (Arduino), OC0A and OC0B, is used for system timing stuff too, so it doesn’t ever go completely “off”. I moved the optocoupler I noted was giving me problems with the ICSP to one of these PWMs- so once the PWM was enabled, it was never at duty cycle 0. That’s not OK, because then the shunt is always sucking a little current. So I need to move it. I think I’m going to move it to PD3 (OC2B) and move what was on there somewhere else. Makes stuff a little less neat, but I think it’s the best option.
Things that need doing in order to order more circuit boards:
- Verify correct operation of communication circuit
- Run long term (2hr) burn test at full shunt power to make sure nothing overheats, gauge the need for heatsinking the power transistor
- Fix power transistor footprint and redesign board and traces, make it smaller. Use 1/8 watt resistors where appropriate
Things that need doing after that:
- Test and plot linearity of analog optocoupler, adjust trimpots
- Get a feel for characteristics of pwm cycle control over shunt current
- Plan firmware
There’s a lot to do. I’m especially concerned with the eventual need to develop the “BatBuss” serial interface, loosely based on “EVILBus”. It’s going to need to be Bit-Banged, and I really don’t have a good idea about how to implement that yet. I’ll figure it out, and I actually don’t even need to to just get the regulators working, but I’m worrying about it anyhow. I also need to get an idea of the characteristics of the REGBUSS on the Manzinita Micro charger, and figure out how I’m going to effectively trigger it to go into Float and Finish modes. I think it will consist of some optocouplers and resistor networks, but I’m not sure yet. Need to test it, and to test it I need some guinea pig batteries and a current meter. An excuse to pick up a nice clamp meter? Possibly.
Battery regulator- part 2
I continued troubleshooting the board yesterday, and came to a few conclusions- The gain of the power transistor is indeed high enough to be driven directly from the optocoupler. In order to get the C-E voltage drop nice and low (.35 v or less) I am driving the base with about 20 ma- it’s definitely saturated. The optocouplers I ordered have CTR 40-80%, so as it is right now, it’s a bit of a balancing act with keeping the OC pulling less than ~30 ma from the AVR pin while maintaining enough C-E current to keep the power transistor saturated. I think next time I order parts I will order higher CTR optocouplers (there are some better ones in the same series of parts) and maybe tweak the resistor values just for a little headroom.
After having gotten that squared away (whew!) I took a quick trip to Fry’s in Sacramento (got very lost on the way. Why are there two different freeways with such similar names?? I80 and Business 80?) to pick up some new resistors for the power transistor base and the optocoupler LED. Was also able to find pinheaders (Yuss!) and a 5v linear regulator. Having all the parts, I finished populating the board.
(Note the upright metal film resistors placed in the TO-92 footprints)
Looks pretty good, right? Well then I couldn’t connect to the microcontroller via my USBTiny and ICSP header. Frustrating. I thought about it overnight and then earlier this morning I confirmed my suspicion that one of the ICSP pins (MOSI in fact) was also being used to drive one of my optocouplers- I assume that was putting enough of a load on the pin that the ICSP was unable to connect.
So, I would say that most of the kinks have been worked out of this hardware! I’m going to take some time now to fix up the schematic and do a little bit more trace reworking on the board so that it’ll reflect the schematic changes. A note- in KiCad eeschema, using wire labels is useful- but if you have labels like Sense 1, Sense 2, Sense 3, they will all be assumed to join together. So don’t include those spaces- I didn’t get this when I was first trying to layout the board so I made wires in the schematic between everything- messy. I’ve fixed it now.
Battery Regulator- part 1
Background: So, I am building this electric car, using SLA batteries and a Manzinita Micro charger. Need battery regulators, have been unable to find a currently available solution, decided to build my own.
This project is virgin territory for me in many areas- circuit design, board layout… but I thought it would be fun, and potentially useful.
On Friday I received my first ever two layer professionally made circuit board! I ordered it through Advanced Circuits barebones service, and it looked like this:
The first challenge went just as planned- see how that RJ-45 jack fits right on there, and how the ATC fuse holder footprint is just fine. It’s been all downhill since there…
The board uses an AVR chip to read the voltage of up to 3 attached batteries. It determines when the batteries are filling up and uses a power transistor and resistor to shunt the charging current so that the other batteries may continue to charge. So the main subsystems are the optocoupled power transistor circuit, the analog optocoupled volatge sensor circuit, and then the AVR support circuits. I’m saving the communication circuit for later.
I decided to start with the power transistor circuit. The schematic I used to make the board looks like this:
If you look at it carefully, it has about 5 things wrong.
-Pinout on 2N2222 is WRONG. This causes the emitter to be attached to ground. In my unwise trust that everything would work on the first go, I attached 12v to the battery terminal, then jumpered +12v to the base of the 2N2222. It popped.
-That’s not actually a darlington configuration. Really. It’s not. That aside, why did I attach the collector of the 2N2222 to the negative bus? What was I thinking!?
-It’s not visible here, but the KiCad stock footprint for a TO-220 has the pin numbers in different places from the actual pinout of the power transistor- so once I tried to test it without the 2N2222, it wouldn’t do anything. No current anywhere- I was a little amazed that I had screwed up two whole pinouts. I’ve definitely learned my lesson now.
So, I did some reworking of the traces, and got it working. Kind of. Current flows freely when the 2N2222 base is energized, and nothing overheats or pops throughout the voltage range of my power supply. BUT when the 2N2222 base is not energized, or pulled low at around 8v input the power transistor starts conducting, up to about .3 amps at 12v. Since it’s not at saturation, it also gets warm, fast. When I disconnect the collector of the signal transistor, this stops happening. So I don’t know.
Consulting the 2SD2528 datasheet (why didn’t I do more of that before?) confirms that it’s minimum beta is 500, so it should draw around 5ma of base current for saturation at 2.5 load amps- I’m pretty sure the phototransistor optocoupler can supply that. So, today I will be working from that angle- maybe what I should have done from the beginning.
And, like the boss I am, I decided to visit my friends in Davis this weekend, brought a lot of equipment but forgot some parts at home- who knew it would be so impossible to get your hands on some SIL or DIL pinheaders on the road! I have billions of ’em at home!
On a positive note, the analog optocoupler circuit seems to work well. Thank you Gordon Stallings! Even though that particular optocoupler is not available, I used a similar one and it seems to work fine. (in fact, there seem to be no DIP package analog opto’s available through Digi-Key. This one is SOT-5, fun!) I haven’t checked linearity yet, but I’m optimistic.
In: Battery Regulator